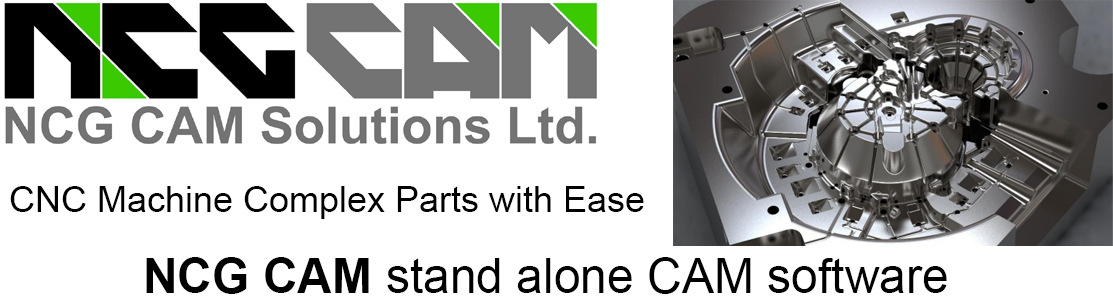
INDUSTRY’S MOST AFFORDABLE HIGH-END CAM SOFTWARE
Starting from $14,500 for Perpetual License
(includes 3-axis milling, 3+2-axis Milling and 2-axis Turning)
Special price for existing PowerMILL users, 3-axis is $10,000
Advanced 5-axis milling additional $9,000
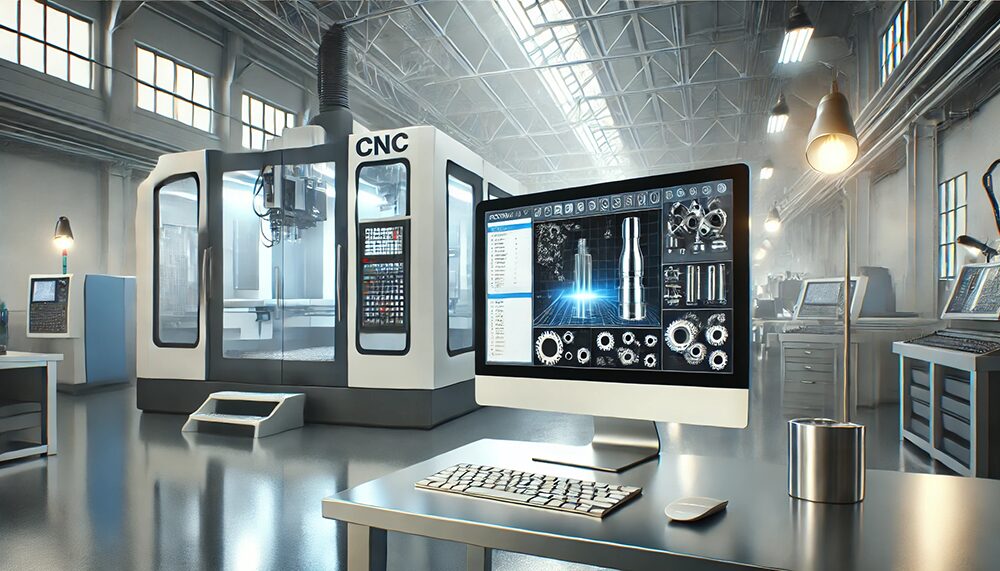


Perpetual Licensing – No Annual Subscription
NCG CAM is a high-end automated toolpath generator for complex part CNC machining. The toolpaths are calculated on a 3D CAD model produced in a 3D CAD software. NCG CAM does only have some 3D modelling capabilities as this is best done in one of the many 3D solids and surface modelling systems available. However some basic surfacing capabilities is available in NCG CAM to better control the toolpaths like preventing the cutter to enter areas not to be machined.
NCG CAM reads all the standard file formats such as STL, IGES, STEP, RAW, CLD and VDA-FS. NCG CAM also interfaces directly with systems like PARASOLIDS, Pro-Engineer, CREO, CATIA and SIEMENS-NX
NCG CAM offers an extensive library of roughing and finishing strategies for producing excellent surface finishes at optimised machining times. NCG CAM is designed for shop floor machining workflow where the machinist has full control of the machining process. This type of workflow provides for large improvements in efficiency and overall part quality. NCG CAM is particularly suited to Mould, Tool and Die applications where accuracy and surface finish is important to minimize subsequent polishing operations.
NCG CAM software offers excellent capabilities in 3, 4 and 5-axis with machine simulation included with 5-axis postprocessors.
A New 2-Axis Turning module is included with NCG CAM 3-axis milling. Support for mill-turn machines is planned for late 2024.
For any CAM software good technical support and training is essential. This applies to NCG CAM too if you want to fully utilise its capabilities and maximise your return on your investment.
Camplex offers full support and training using on-line and face-to-face learning.
Strengths & Features:
-
Adaptive Clearance Roughing using full flute length of the cutter
-
Powerfull Rest Roughing from Stock Model or existing toolpaths
-
Core & Cavity Roughing
-
Flat Area Roughing and Finishing
-
Fast Stock Model Calculation
-
Finishing using Waterline, Raster, Helical and more
-
Rest Milling using reference cutter or toolpaths
- Rest Milling using calculated stock model
-
Corner and Pencil Finishing
-
Toolpath Animation/Simulation
-
Machining in 3-axis, 3+2-axis, 4 and 5-axis
-
Fully gauge protected cutter and holder
-
Toolpath editing for optimum efficiency
5-axis Capabilities:
-
Full Gouge Protection against cutter and holder
-
3-axis to 5-axis Conversion with gouge protection
-
5-axis Roughing
-
Parallel Machining
-
Swarf Machining
-
Morph Machining
-
Flank Machining
-
Support for Barrel Milling Cutters (3,4 &5-axis)
-
Machine Simulation in Machine Model

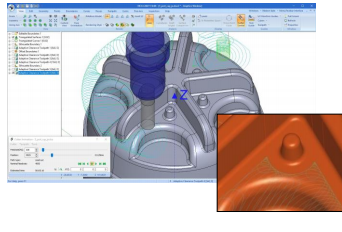
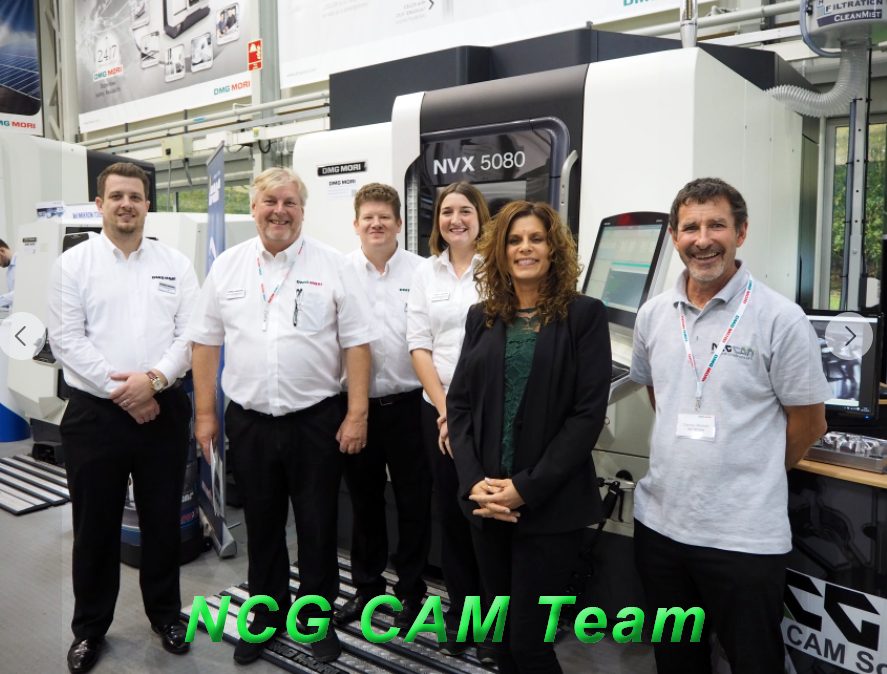
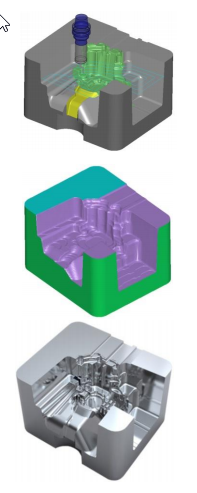
Other Features
A unique machining feature is adaptive area clearance which eliminates full width cuts using a concept similar to trochoidal milling. This cutting technique is aimed towards high speed machining with solid carbide cutters. It provides the ability to safely cut using the full length of the flute at the optimum cutting speed for the material and part. Tool wear is spread evenly, cutting more on the flute than the bottom of the cutter, reducing deflection and the potential for vibration by maintaining a constant load on the cutter. The technique is particularly suitable for cutting hard materials and also some electrode manufacturing. The strategy automatically adjusts the toolpath for efficient and safe machining, improving cutting conditions and allowing more consistent and possibly higher machining speeds to be maintained.
As well as significantly improving tooling life, adaptive area clearance can reduce machining time by an average of 25% over conventional roughing as the machine uses the full flute length of the cutting tool, and the machine runs at the optimum speed without exceeding its limits at an isolated point.
NCG CAM features optional 5-axis milling is used to finish hard to reach areas. 5-axis machining allows for the use of shorter cutters, resulting in less vibration and better surface finish.
NCG CAM fully gouge protects the cutting tool and the tool-holder, which is very important when you may have a tool-holder and/or tool that is not long enough to reach. Likewise, it also provides gouge protection when machining using 5-axis machine tools ( 3+2 axis ), and machining areas which might be deemed inaccessible with the standard 3-axis approach.
Software and Milling Demos
High-Speed Milling Strategies with DMG-Mori